- Reaction score
- 10,329
I have an ECU that has 2 x corroded pins that have broken clean off. It's from a jet ski and a new ECU isn't an option. At some stage sea water must have leaked past the seals on the plug and the rest is history 
The ECU is a hard plastic enclosure and it's filled with a high density rubber potting agent of some kind so I really don't fancy my chances of being able to open it up without damaging it.
Just wondered if anyone had any ideas on how I can repair the pins. They've broken off flush with the back of the socket so there's nothing protruding that I can solder to. My best plan was to take it to a watch maker and see if he could drill and thread the broken pins and screw on an extension pin but I think this would be a long shot.
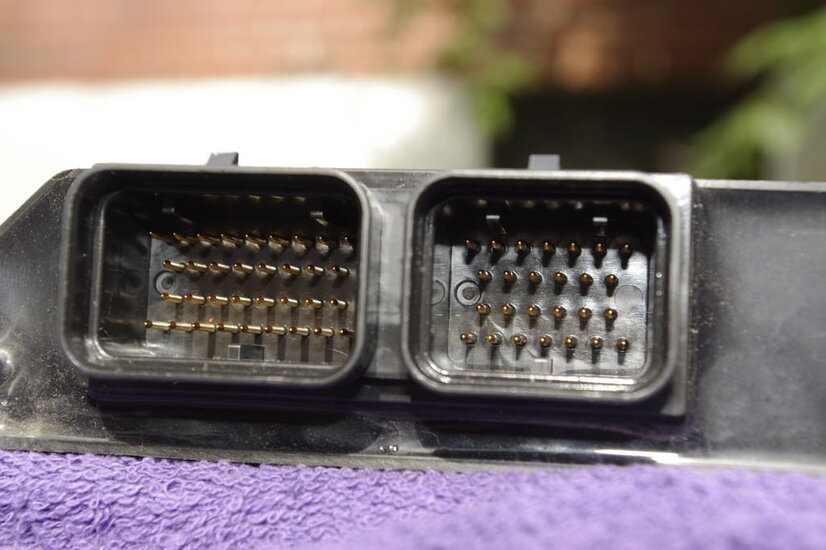
This is what the socket would look like in good condition
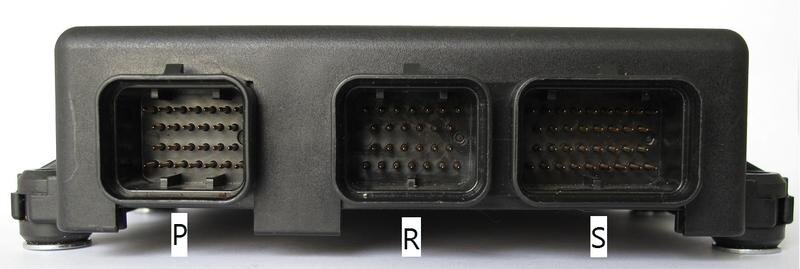
This is what the back of the ECU looks like.
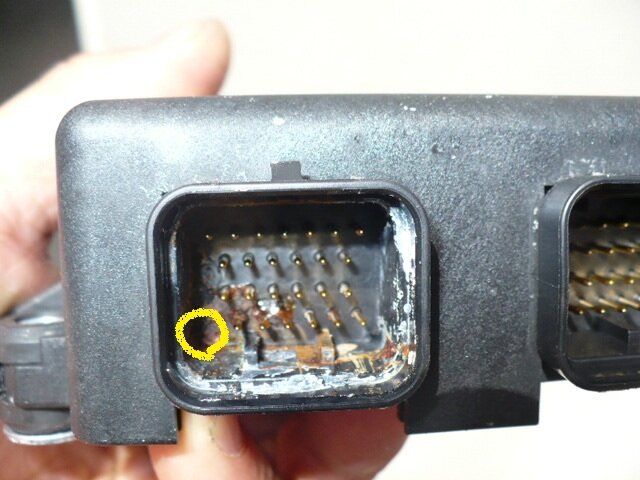
This is what the corroded socket looks like.
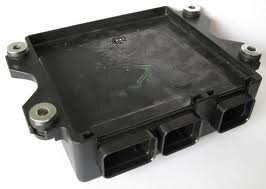
The ECU is potted in solid rubber.
The ECU is a hard plastic enclosure and it's filled with a high density rubber potting agent of some kind so I really don't fancy my chances of being able to open it up without damaging it.
Just wondered if anyone had any ideas on how I can repair the pins. They've broken off flush with the back of the socket so there's nothing protruding that I can solder to. My best plan was to take it to a watch maker and see if he could drill and thread the broken pins and screw on an extension pin but I think this would be a long shot.
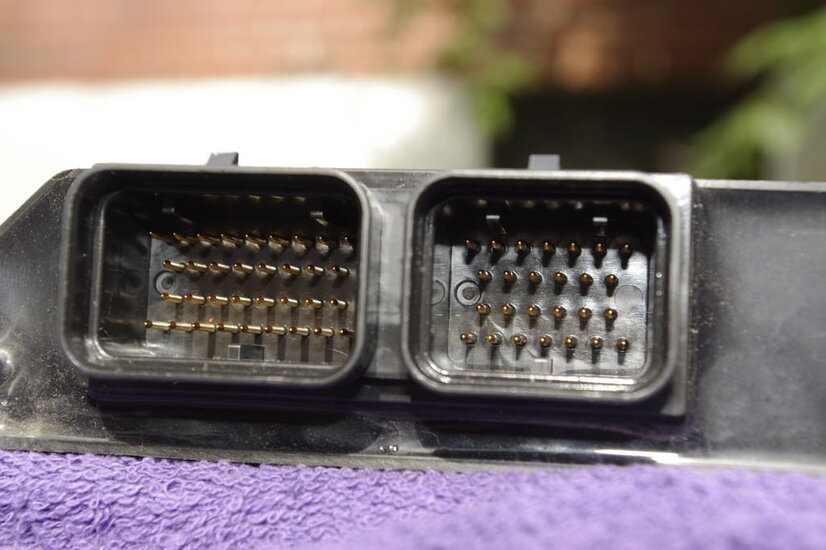
This is what the socket would look like in good condition
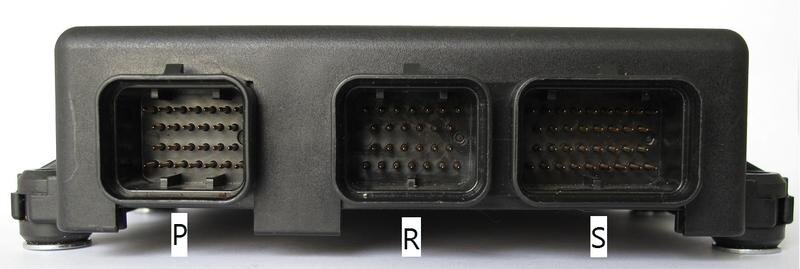
This is what the back of the ECU looks like.
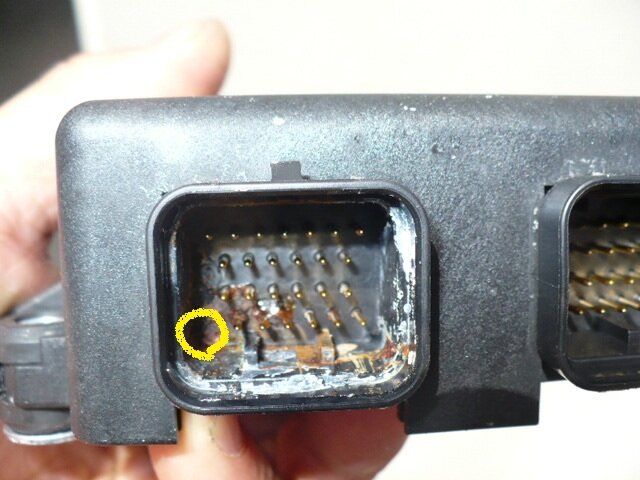
This is what the corroded socket looks like.
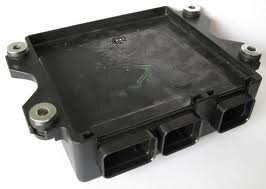
The ECU is potted in solid rubber.